ダイバーの理想を叶えることがメーカーとしての使命です。 〜総合スーツメーカー・ワールドダイブ高橋さんインタビュー〜
ドライスーツ国内No1シェア
ワールドダイブの魅力にせまる!
先日、ドライスーツが苦手……不安……と「ドライスーツの壁」に途方に暮れている方のために、ダイビングの総合スーツメーカー「ワールドダイブ」の担当者の方にドライスーツのお悩みについて聞いてきた編集部。
ドライスーツのお悩みの多くは「使い方」で解消されること、また、それを補える「素材」も準備されていることに目からウロコ……!
素朴な疑問にもさっと回答が出され、そして、ちょっとした悩みにも真摯に向き合う姿に感動しました。
そして、スーツメーカーがダイバーの動きをここまで想定してドライスーツを製作していたとはっ!!
ワールドダイブといえば、ドライスーツの国内シェアが約46%(2017年データ)を占めるという、実力派メーカー。
“国内トップシェア”を誇る陰には、どのような努力が隠されているのでしょうか?
創業から40年を超える老舗スーツメーカーの「ワールドダイブ」に、改めて、モノづくりへのこだわりを聞きたい!
ということで、ワールドダイブに勤めて24年。
現在、取締役としてワールドダイブを支え続けている高橋信弘さんにお話を伺いました。
それぞれのダイバーが求めることを叶えることが
ダイビング総合スーツメーカーとしての使命
--
ワールドダイブは、どのようなダイビングスーツ作りを目指していらっしゃるのでしょうか?
高橋
一口にダイバーと言っても、それぞれ体型も違えば、寒がり暑がりなどの感覚も違うし、運動好き嫌いなどの性格も違います。さらに加えて、ダイビングスタイルや環境も違うわけで、まったく同じ状況のダイバーっていないのです。
突き詰めていくと、「ダイバー1人ひとりに専用のスーツがあったほうがいい」という結論になります。
さらにいうと、体感もそれぞれ違うので、春はこれ、夏はこれ、といった季節専用のスーツがあれば理想です。季節によって洋服を着替えるようにスーツも季節が変われば着替える、人それぞれにあった形がある、ということです。
--
それってもう、求め出すと“無限”になってきますよね?
高橋
はい、無限ですね。ですが、可能性も無限です!
なので、それを最大公約数的に今自分たちが手に入る素材や技術で理想のスーツに近づけ、それらが毎年発表されるカタログに集約されます。
今のアイテムでカバーできるところもありますが、もちろん、カバーできないところもまだまだあります。最終的には「うちのカタログを見てもらったら、どんなダイバーの要望に叶うものも全部用意できます」というのが一番理想。今は、それを目指している途中で、まさに終わりのない旅みたいなものですね……。
--
そういった意味で、ダイビング総合スーツメーカーと“総合”という言葉にこだわりを持っていらっしゃるのですか?
高橋
ダイバーそれぞれが、もっと快適に潜れて、楽しみの幅がもっと広がればいいなと思っているんです。つまり、「人それぞれに合ったストレスフリーのスーツ」を作っていきたい。ストレスをなくし、問題解決を導くような……。
そんな完成度の高いスーツを作るためには、常に進化し続けなければなりません。なので、社員全員、高いところに基準を持ってモノづくりに取り組んでいます。
手作業が中心のスーツ作り
「品質の均一化」のために考えることとは?
--
スーツはどういった工程で作られているんでしょうか?
高橋
基本的には手作業でスーツ作りを行っています。まず、型紙を作って、生地を切って、貼り付けて……。
時間も手間もかけて、愛情込めてスーツを作っています。
一方で、「人の手」で行う手作業は、作業に“ムラ”ができ、完璧に同じものを作るということはすごく難しいという側面もあります。
その点、品質の均一化を図るため、機械化できるところはしてきました。
1980年代にまで遡りますが、時期により納期が変わってきてしまうことがありました。たとえば、注文が殺到する夏の繁忙期には納期が1か月以上とものすごく遅くなって、冬場は納期が早いなど、ですね。こうしたことは、当たり前で混んでいるのだからしょうがない、という空気がスーツ業界ではありました。
でも、私たちとしては、欲しい時期に欲しいユーザーさんに品質の良いスーツを届けたい、という思いがあります。
そこで、手作業でボトルネックになっているところを機械化して、効率的に均一化を図り、高い水準を保つということを、まずしなければいけないなと。
1984年には、業界に先駆けて、設計や製図のシステムソフト「CADシステム」を導入しました。恐らく業界で一番最初だと思います。これにより1着の製図時間が約2時間かかっていたものが、数分で出力できるようになりました。
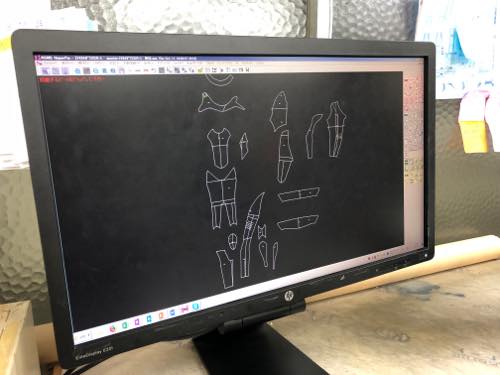
設計や製図のシステムソフト「CADシステム」!
ただし、出力したものをすべてそのまま使えるというわけではなく、そこから体型に合わせて手直しが必要なものもあり、最後はやはり人間の手で仕上げる、という工程はまだ残っています。
しかし、こうしてCADを型紙製作に使用することで、“型紙を作る”という工程を大幅に短縮できました。ただ、これらの作業が効率的にできるようにするためにその前段階として、1品番ごとに膨大なデータを入力して、プログラムを完成させておかなくてはならないので、単純に時間が短縮できたというわけではないのです。しかもその中でもやはり精度というものが非常に重要になってきます。
さらに、自動裁断機「CAM」を導入し、CADのデータをCAM用のデータに変換したものを入れたら直接切ることができるようになり、作業効率と裁断精度がさらに上がりました。
また、CADを導入してからすぐに作業効率がアップしたわけではなく、さらにそのCADを使って「既製サイズの充実化」を図っていました。
通常の既製品って、S、M、L、XLなどでサイズ分けされていますが、当時はウェットスーツの既製サイズだけでも33サイズを用意していましたし、それが今では51サイズになりました。
選びやすいようにサイズ早見表のようなツールも作ったりして既製サイズの利用率を促進していきました。こうして事前に型紙を工場へ保管しておくことで「型紙製作」という工程を少なくして「型紙待ち」という滞留時間を減らして納期短縮をしていました。
--
え、既製サイズが51サイズ? 試行錯誤してきた背景がうかがえますね。
高橋
クオリティの均一化、そして、職人の負担軽減のために導入した機械もあります。 スーツ製作には、生地と生地を接着剤でくっつける工程があります。貼り合わせる時は、生地の断面をつぶさないように指の力の入れ方に気をつけなければならないし、貼り合わせたあとは人差し指にかなり力を加えなければいけないので、指に負担がかかる作業なのです。そのような作業をしていくことで職人さんの人差し指が中指側に反って曲がってしまうことも……。
そこで創業者の高田が、指の負担を最小限にして生地と生地をくっつけるけることができる「エアーニッパー」を考え出しました。これはコンプレッサーから送られてくる空気を利用して生地を挟み込むもので画期的でした。いろいろあって特許はもらっていませんが(笑)
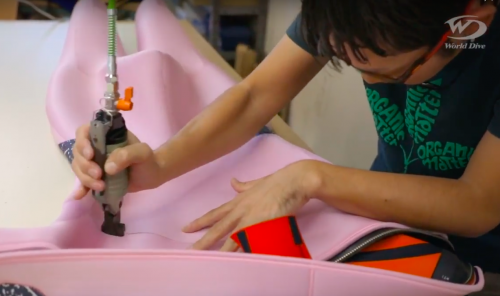
エアーニッパー。「圧縮空気」を利用し、貼り合わせた生地をしっかりと繋ぎ合わせる
おそらく今はどのスーツメーカーさんの工場でも、結構使われているのではないかと思います。
品質を保ちつつ、職人たちのストレスを削減しながら、どれだけ早く完成させられるかを常に考えております。 スーツ製作において、とにかく求められるのは「品質の均一化」なのです。 それを高いレベルでどこまで保っていけるかが勝負ですね。
ただ、「人が支えている」っていうのは、モノづくりの基本です。そういった本質はぶれずに、これからも最先端の機械などいち早く導入していきたいです。
ワールドダイブは徹底的にやりぬく!
素材との“出会い”を求めてとにかく動く
--
ワールドダイブが、他のメーカーさんにここは負けてない!というところを教えていただいてもいいですか?
高橋
いろいろありますが、一番わかりやすいのは「裏地」ですね!
一般的な起毛素材っていうのは「中空糸(ちゅうくうし)」といって、真ん中が空洞になっている糸で生地を作ります。そうすると、フワフワしたものになるので、水ハケが早いから乾きも早くなり、ダイビング後の冷えが軽減されるんです。
ただし、素材に空洞が多いので、着用して潜っているとスーツと体の間の水が動いてしまいます。ウエットスーツの場合、スーツと体の間の水を体温で温めて保温しますが、この生地だと十分に水が温まる前に水が動いてしまうのでダイビング中の保温力を落としてしまいます。水が早く抜けて乾きも早いので、サーフィンのような水面のスポーツには非常に適している生地だと思います。もちろん、スタンダードジャージのスーツに比べたらいいものには変わりないのですが……。
ワールドダイブのスーツの裏地は、「マルチエラスチックス」という素材を使用していて生地の厚みと密度が違います。この素材は、ダイビング中に入ってきた水をびっしりと密集した繊維がしっかりとキャッチして、水を動きにくくしてくれます。
スーツと体の間に入った水を逃さないため、体温で水が温められて保温力が高まります。
ドライスーツの場合も目付量の多い素材は断熱剤としての機能も大いに発揮し、また肌触りが良く、着脱もスムーズにできて、しかも水中でスクイズがかかった時に滑らかに滑ってくれるので、スクイズの強い締め付けも緩和してくれます。
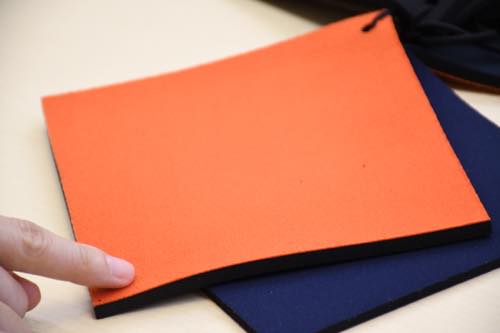
これがトップシェアの裏地。肌触り抜群で、なんだか優しい……。
次に問題になってくるのが、「動きやすさ」です。
ドライスーツは水を完全に止めるという機能が重要になります。そのため、水圧下で繰り返し使用してもゴムがへたらないようにして水漏れのリスクを低くする必要があり、ウエットスーツよりも硬い強度のあるゴムを使用しなくてはなりません。ただ、そうするとウエットスーツの生地よりも動きづらくなってしまいます。
そこを改善するために2004年に新たな特性を持ったゴムを導入しました。
それまでのドライスーツ用のゴムは耐久性だけを重視して選定していたので、動きやすさということはある程度目をつぶっていました。しかし、ダイバーのダイビングスタイルや思考が変化して、ドライスーツにも「動きやすさ」と「耐久性」という相反する2つの要求も高まってきて、現在の伸縮性も耐久性も高い「動きやすくてヘタリにくい」ゴム素材を採用することになりました。
そこに生地の機能がプラスされ、高い保温性能と運動性能をアップする相乗効果として現れてきます。
--
まさにノンストレスに近いスーツですね。でも、どうやってこのように求めている素材を手にいれているのでしょうか?
高橋
シンプルですが、とにかく動くことですね(笑)
ゴムに関していえば、なるべくゴム屋さんや加工屋さんに直接交渉しています。 問屋さんから仕入れれば早いのですが、それだと「オリジナル」を作ることは難しくなります。 仕入れ先とたくさん繋がりを持ってこちらの意図をしっかりと伝えて、ゴムならここ、ジャージならここ、といったように、各部が求める素材が手に入りやすくなりますよね。 地道なことですが、そうやって足を運ぶことによって「オリジナル」を作っていっています。
--
そういう素材との“出会い”が、いいスーツを産んでいるのですね。
やらなきゃわからないでしょ!
スーツ作りのためにフリーダイビング実体験
--
現在、フリーダイビングの選手に向けて、専用のスーツを提供しておられるとのことですが、どのようなことで苦労しましたか?
高橋
フリーダイビングのスーツって2mmや3mmほどしか厚みがなく、とにかく伸びるんです。
スキューバダイビング用のスーツとは全然違うので、何がどうやったら快適になるのかわからなくて、フリーダイバーのHANAKOさんにも協力してもらい着用して使ってもらっても、やっぱり後からここが違うとかでてきてしまってうまくいかなくて……。なかなか納得できるスーツができなくて悩みました。
なので、これはもう、俺たちもフリーダイビングするしかないと!!
ということで、プールでHANAKOさんに実際にフリーダイビングを教えていただきました。
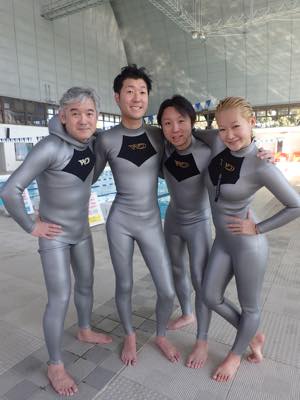
フリーダイバーのHANAKOさんの協力を得て、フリーダイビングを実体験!
--
わからなければやるしかないと(笑)なかなかの体育会系で……。
高橋
でも、実際体験してみると、やはり求める素材や作り方っていうのが見えてきたのです。ヒヤリングをしながらモノを作ることも非常に重要ですが、実際に体験してみないと細かいニュアンスやちょっとした違いが非常にわかりにくく、こうしたことを体感して得られたということはとても大事だと改めて実感しました。
やっぱり、なんでも体験しないとわからないですね。
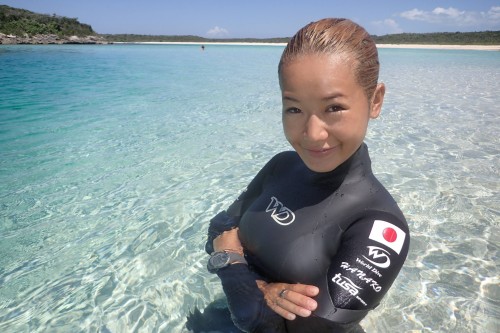
2018年バハマで行われたフリーダイビング世界大会「バーティカル・ブルー2018」にて世界記録(106m)を達成! スーツにはワールドダイブのマークが輝く。
--
いいスーツを作るためにどこまでも追求する徹底さ、そこへの地道な努力。なんだか感動しました。
理想を追い求めるワールドダイブ
次に発信していきたいスーツとは?
--
それでは最後に、ワールドダイブがこれから作っていきたいスーツはどのようなスーツでしょうか?
高橋
現実的に今は難しいので理想の話になっちゃいますが、ストレスフリーを追求するならやっぱり「着脱のしやすいドライースーツ」ですね。
ウエットスーツは「SCDシリーズ」といって、長いファスナーを使用した着脱のストレスを激減するデザインをすでに導入しており、人気商品となっています。
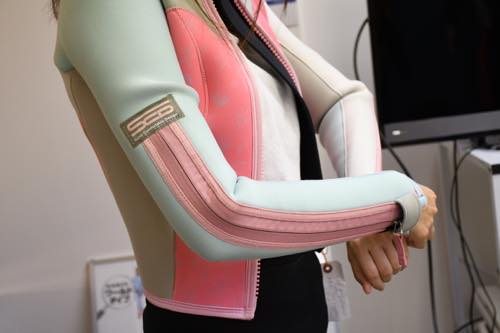
「SCDシリーズ」のウエットスーツ。着脱がとにかくスムーズ!
それをドライスーツでやるとなるとかなりハードルが高いのですが、ダイバーに絶対的に求められている部分ですし、必ずヒントはあると思っていますので実現できるように取り組んでいきたいですね。
理想のお話ですが、でも、そういうことを発信していくのも、メーカーの使命だと思っています。
これからも、その「理想」を追い求めて走り続けていきます。
--
なんだか夢があって素敵です。でも、ワールドダイブのパワーで実現してしまいそうですよね。着脱のしやすいドライスーツ、楽しみに待っています!
■supported by ワールドダイブ
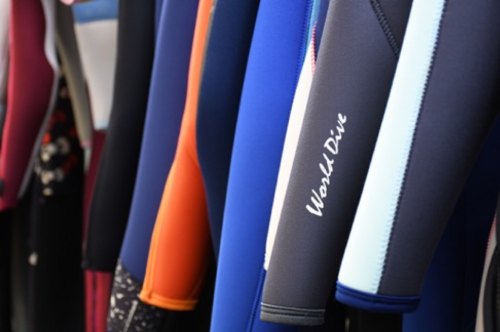
「あらゆる環境で快適なダイビングライフをお届けすること」をモットーに、国内生産にこだわり、自社の工場でスーツを製造している総合スーツメーカー。設計、素材、装備、そして技術のすべてにおいて、現在得られる最上のクオリティで仕上げ、その名の通り世界の海で通用するスーツを作り上げている。
\期間限定ドライスーツ発売中!/
\ワールドダイブの記事をもっと読む/